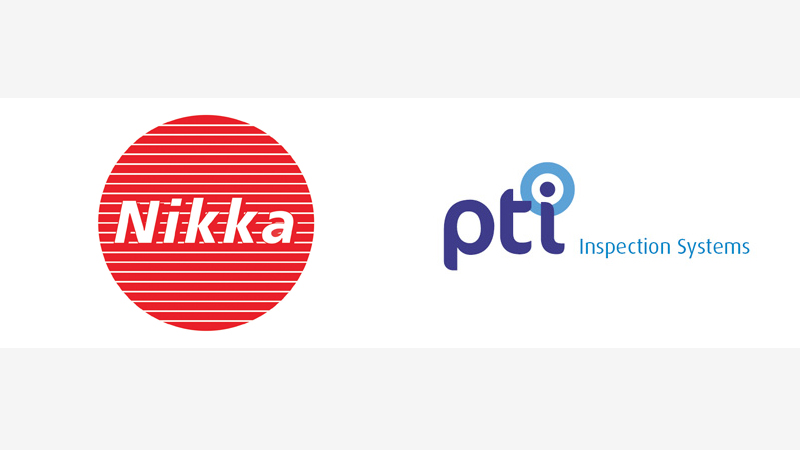
Leak Detection of Pre-Filled Syringes
Recent years have seen a significant rise in the use of pre-filled syringes (PFS) as a containment solution for pharmaceutical products. This trend is expected to accelerate over the coming decades. For the pharmaceutical company, the advantages of prefilled syringes are minimizing drug waste and increasing product life span.
Register NowDownload DocumentRecent years have seen a significant rise in the use of pre-filled syringes (PFS) as a containment solution for pharmaceutical products. This trend is expected to accelerate over the coming decades. For the pharmaceutical company, the advantages of prefilled syringes are minimizing drug waste and increasing product life span. For healthcare workers, prefilled syringes are recognized as an efficient, reliable and convenient method for drug administration. Furthermore, many injectables can be self-administered without the concern of complete transfer from a vial. This gives rise to a safe and efficient option for patients requiring long-term pharmaceutical therapies.
However, from an inspection perspective, the PFS gives rise to a new set of criteria to be considered. With the method of delivery being as important as the product, we see an ever increasing overlap between the world of medical device and pharmaceutical manufacture. In the field of container closure integrity inspection (CCIT), prefilled syringes offer more complexity when compared with the traditional vial. For a PFS, there are more pathways and possibilities for a containment breach to occur as we consider the barrel, needle, plunger and seal ring.
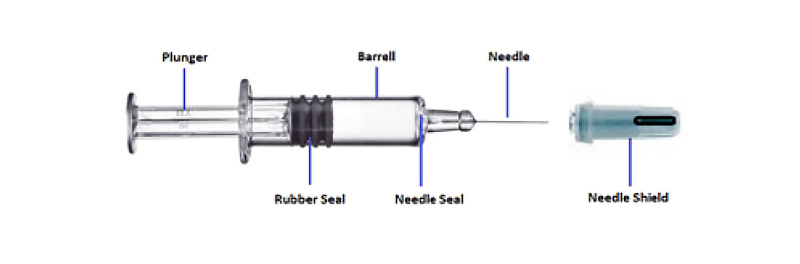
A key consideration when considering the PFS for inspection is the distinction between quality issues and container integrity issues. For example, the needle could be slightly bent within the shield but may not have pierced the cap. In this case the PFS would clearly fail on quality but from a container perspective, there may not be a breach through to the liquid inside. Another frequent example on this is the rubber seal on the plunger. Typically this has ribs or fins which act as container integrity seals. If liquid has passed the inner fin but not the middle or outer, again this would be a quality fail but the closure integrity may well still be intact. This distinction means that it is important that we consider CCIT as a subset of overall package quality.
From a CCIT perspective, one of the best technology solutions to use for PFSs is High Voltage Leak Detection (HVLD). HVLD is non-destructive which is an important consideration when you want a test method that is both 100% and repeatable. HVLD is also deterministic in that it offers both historical and real time data that can be assessed against pass/fail criteria, thus eliminating the subjectivity of human visual inspection.
HVLD works by briefly applying a voltage across the syringe. In the event that the PFS has a containment breach through to the liquid, there will be a significant change to the resistance value between the test electrodes. This creates a recordable change in the value of current/voltage in the test device.
However, significantly, where HVLD works particularly well for pre-filled syringes is that it is able to detect failures from multiple different sources by moving either the test electrode or the PFS to focus on a particular area.
- If the glass/plastic barrel is cracked or has a pinhole, this will be detected easily.
- If the liquid has leaked passed the rubber seal on the plunger, this can be detected by bringing an electrode close by. However, if the defect has not breached all of the fins there may not be a pathway from the liquid through to the environment, and so this may need to be picked up on a quality inspection rather than a container closure integrity test.
- If the needle seal is compromised, any leak path through to the inside of the needle can be detected.
The needle creates an interesting situation for CCIT. If the needle bends and pierces the inner soft shield but does not pierce the outer cap, then two issues here need to addressed. Firstly, this bending of the needle may result in damage to the needle seal inside the barrel. If a leak occurs here, this can be detected by HVLD. But also, a HVLD system may be able to detect the needle having pierced only the inner soft cap. Many PFS hard caps now have windows or holes. In this instance, the needle will offer a low resistance path due to the repositioning of the metal. This allows HVLD to be used to detect needle bending for many PFS types, depending on the design of the hard cap.
Possible solutions when looking at HVLD as a solution for PFS testing include:
The PTI E-Scan655 offers offline HVLD testing for prefilled syringes.
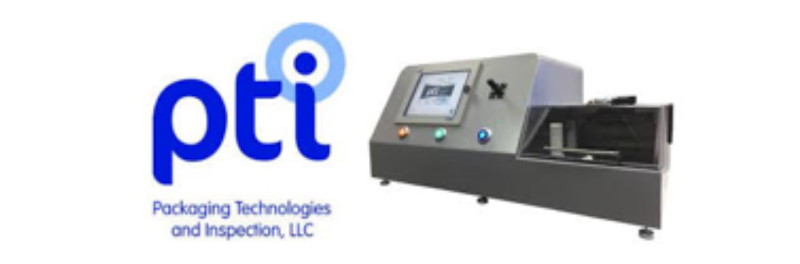
The Nikka Densok HDT offers inline HVLD testing for prefilled syringes.
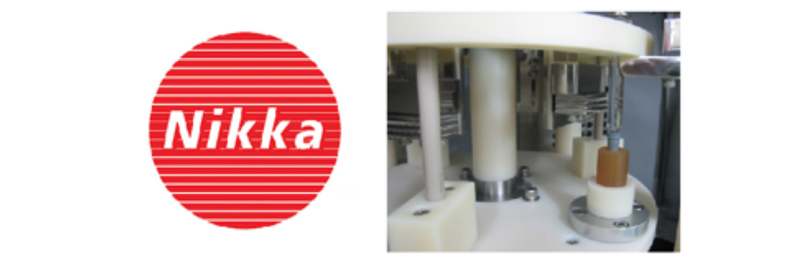
To find out more, or arrange an appointment with your local Technical Sales Manager, email Laura Sheahan at lsheahan@ippgroupltd.com