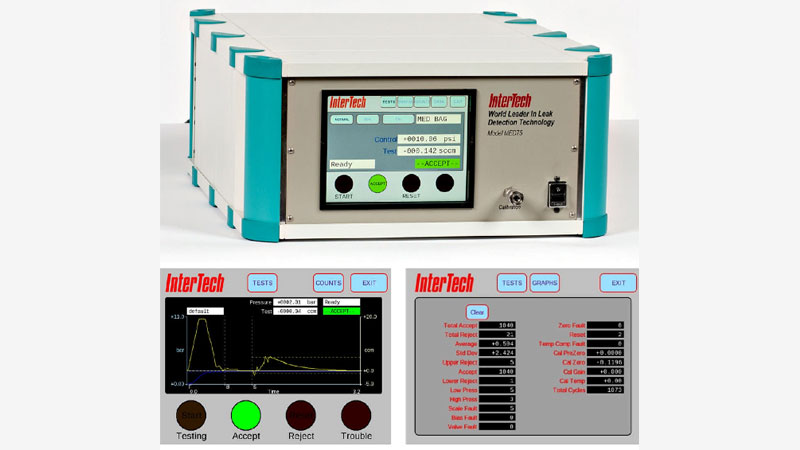
Leak Testing – A faster and more cost effective approach
New product innovations in the medical device industry drive an ever-increasing demand for faster and more reliable leak testing. From legacy products such as catheters to the modern developments in pressurized wound dressings, the challenge always remains to find more efficient and reliable test methods in order to reduce cycle times while still maintaining reliability in the quality of the test method.
Register NowDownload DocumentNew product innovations in the medical device industry drive an ever increasing demand for faster and more reliable leak testing. From legacy products such as catheters to the modern developments in pressurised wound dressings, the challenge always remains to find more efficient and reliable test methods in order to reduce cycle times while still maintaining reliability in the quality of the test method.
One approach to achieving this goal is to consider the application of mass flow detection over traditional pressure decay .Many in the industry treat pressure decay and leak testing as interchangeable terms. Indeed, pressure decay has been the most common technology used to test for leaks in products for many years. So what is the difference between mass flow and pressure decay in the context of leak detection?
Pressure Decay
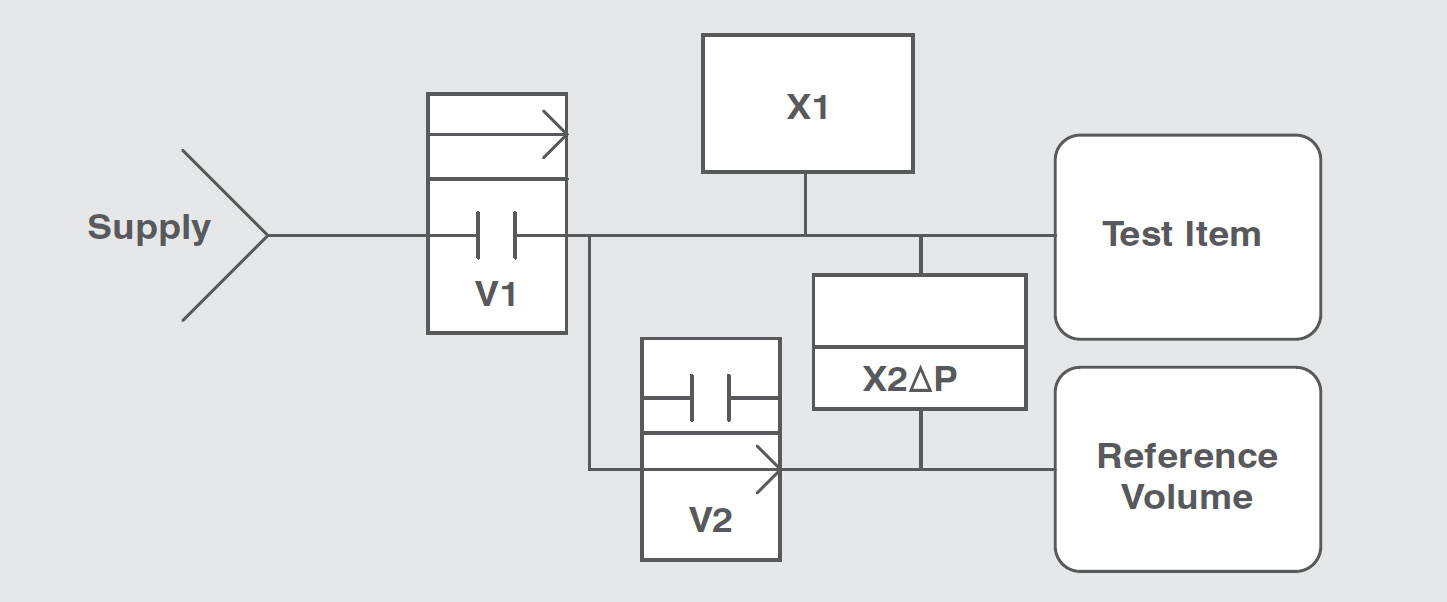
Pressure Decay/Differential Pressure: Test item and non-leaking reference volume are pressurized from the same air supply, then both are isolated by closing V1. The reference volume is isolated from the test item by closing V2. The pressure transducer X2ΔP reads pressure differential between reference volume and test item. Pressure differential is then converted by calculations to provide a measure of leak rate.
The primary drawback to this solution is that two measurements are required, one at the start of the cycle and the other at the end. Time is needed between these intervals to allow the system to equalise after the introduction of pressure into the test item. The longer the interval required, the longer the test cycle takes. Also, longer intervals lead to a decrease in accuracy as the rate of change in pressure decay reduces over time.
The other issue that needs to be accounted for with pressure decay is the influence of adiabatic effects on the system. Because a measurement system based on pressure is intrinsically linked to the temperature and volume of the system, any changes in temperature will affect the accuracy of the system.
Mass Flow Detection

Mass Flow: Test item and non-leaking reference volume are pressurized from the same air supply line, then both are isolated by closing V1. The reference volume is isolated from the test item by closing V2. Then the mass flow sensor X3 reads flow of air moving from reference volume into leak test items, thus providing a direct reading of leak rate in standard cubic cm per second.
This approach yields two advantages over pressure decay testing. The first being that this method only requires a single measurement, so it eliminates any inaccuracies resulting from rate of change of decay over time. Also, the instantaneous reading means that the method is not as sensitive to changes in uncontrolled variables such as temperature over time.
The other advantage of this approach is a significant reduction in test cycle times. The two measurement requirement for pressure decay followed by a calculation to produce a leak rate, not only creates added opportunity for inaccuracy, but also takes more time. Updated mass flow sensors give the most rapid and direct measurement of leak rate because they can be finely tuned to more responsive and quicker in any given application. Test cycle time reductions of up to 30% have been achieved.
To see if your leak test cycle times can be reduced, saving you time and money, why not contact us to find out more information. We offer a range of Intertech solutions using advanced mass flow sensors that can offer fast and accurate leak testing.